OVERVIEW
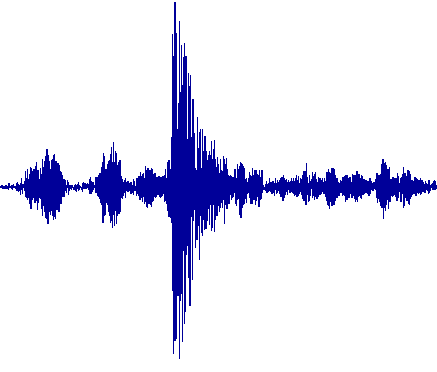
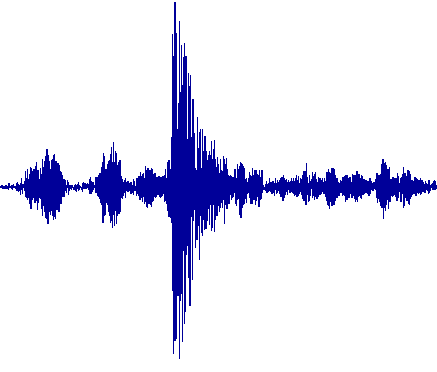
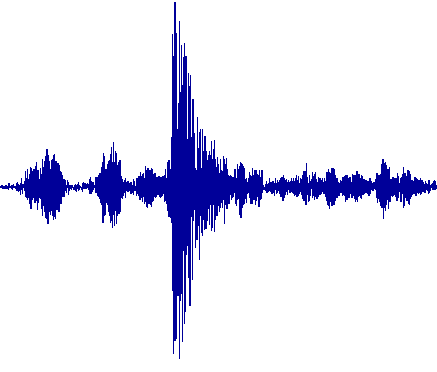
AUTRONIC ENGINE KNOCK CONTROL
If you have an Autronic Engine Management System equipped engine that is operated with a fuel which requires ignition timing retard to prevent damaging combustion knocking, then the addition of knock control can offer the potential for performance gain without any loss of engine durability. The larger the retard that is required for safe operation, the larger the performance gain possible. The performance gain comes when ignition timing for each cylinder is instantaneously adjusted to the minimum retard that allows only infrequent light knocking. Multicylinder engines show larger gains than single cylinder engines because of cylinder to cylinder mismatch compensation. Gains achieved usually range from 2% to 5% for a naturally aspirated engine, and 3% to 10% for an exhaust driven turbo-charged engine. Larger gains have been reported by customers with heavily knock limited engines. The earlier ignition timing achieved, provides the additional benefits of reduced brake specific fuel consumption (BSFC) and reduced exhaust gas temperature giving lower exhaust valve and exhaust system temperatures. In exhaust driven turbo-charged applications, reduced temperatures and the reduction of back-pressure associated with the reduced gas temperature extends component life and are responsible for the larger increases of engine output typically seen.
Our affordable combustion knock control add-on for SM3 and SM4 wire-in and SM4 based plug-in ECUs features modern DSP (Digital Signal Processor) technology that offers impressive performance from surprisingly simple hardware. Its high performance DSP technology adds versatility to all aspects of the combustion knock detection process. This product is a true cylinder by cylinder knock control system for applications up to 12 cylinders using one or two vibration sensors. Its capability extends to multiband signal filtration with agile rpm and crank angle dependant adaption for both signal capture window and filtration frequencies.
Its complex multi-band adaptive signal processing provides improved discrimination of knock signal from background noise. This extended capability copes better with the elevated noise levels of high RPM engine operation and noisy engine modifications such as aggressive valve train components and forged pistons. When compared to OE narrow band sensor systems, we have seen that our system, when used with a broadband vibration sensor, shows significant improvement in knock discrimination ability.
Intelligent diagnostic functions support failsafe and limp-home strategies for various abnormal conditions including poor signal quality, sensor or sensor wiring failure.
Built in cylinder by cylinder adaptability allows this product to be factory pre-programmed with calibrations that suit whole engine families not just a particular engine. Interchangeability is similar to OEM ECU knock systems.
Use this system as a tool to aid in the development of optimal heavy load ignition timing maps by pushing the ignition timing of each cylinder to the threshold of knock control intervention.
This product is supplied as pre-programmed modules to suit specific engine types. Since they require no user calibration, these units do away with the laborious selection process for signal filters, detection window angles and sensitivity calibration maps. Routine engine changes can be made without making any adjustment to the Knock Processor Module or ECU.
Calibrations for new engine types that are not in our library are developed in response to customer requests. We can provide a service to develop a calibration for your engine. A calibration can only be developed if we are provided with quality sound recordings of your engine operating with and without the presence of knock.
!!! WARNING !!! This module and knock control system is designed to limit knocking intensity and frequency. It cannot totally eliminate knocking. DO NOT APPLY to engine types that cannot endure light intensity knocking under high load operation.
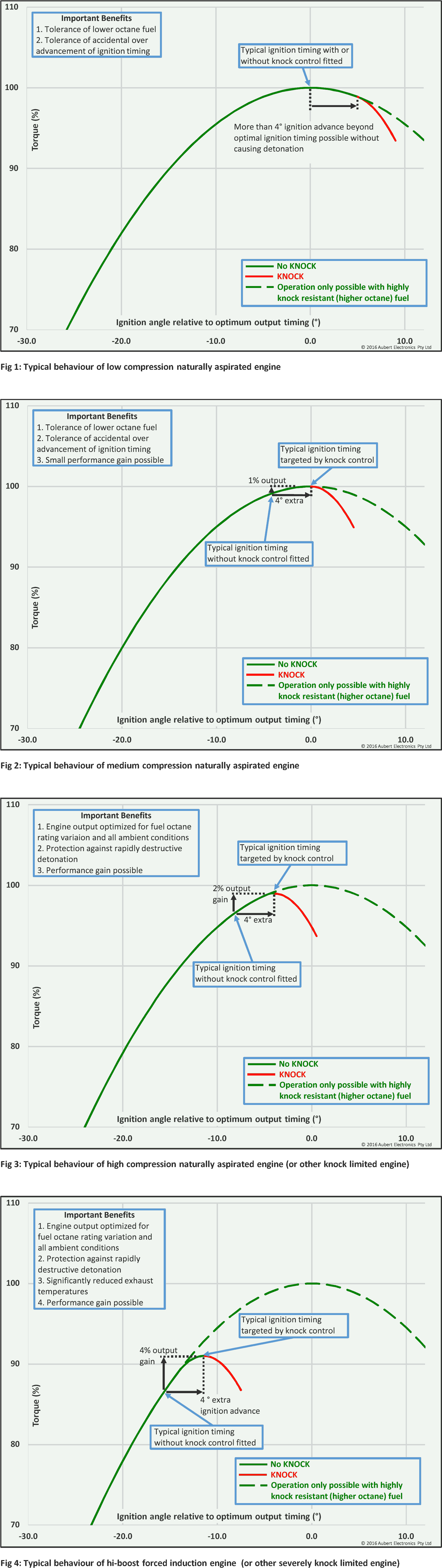
ENGINE KNOCK
Knock is the term used to describe the rapid/uncontrolled combustion of the air/fuel mixture that is ahead of the expanding main flame front. The phenomena is given the name knock because of the knocking sound that is almost always heard when the abnormal combustion occurs. This abnormal combustion usually occurs at the extremities of the combustion space in the last part of the air/fuel mixture to combust. This rapid/uncontrolled combustion produces high rates of pressure rise and high pressures that are mechanically damaging, and high gas speeds associated with pressure wave phenomena. The high gas speed transfers a large portion of the combustion heat to combustion chamber surfaces resulting in considerable power loss. At low engine RPMs cylinder head gasket, piston crown or ring land or ring groove, piston ring, cylinder bore, connecting rod or bearing damage or failure will result if severe knocking occurs. At higher RPMs there is also the likelihood that thermal overload will weaken and then erode or melt the piston crown and/or combustion chamber, resulting in extremely rapid engine failure.
This knocking occurs in spark ignition engines when mixture temperatures exceed the auto ignition threshold of the fuel. High engine and/or air temperatures, low relative humidity, high compression ratio and heavy load or boosted conditions are all factors that force operation beyond the tolerance of the fuel. This tolerance property of a fuel is known as its ‘octane rating’.
Most engines are constructed with characteristics that can result in knock induced damage at heavy load if operated in an uncontrolled manner. This is generally because a high compression ratio is chosen to improve efficiency at part load where an engine most often operates. These engines use spark ignition retard and/or air/fuel mixture enrichment to reduce end mixture temperature below critical levels during heavy load operation. An engine that commences knocking before the ignition timing can be advanced to the optimum angle, is said to be ‘knock limited’. If the fuel octane rating is high enough, optimum ignition timing advance can be applied without knock occurring and engine operation can then be described as not ‘knock limited’.
Older production engines without an automatic knock control means, must use enriched mixtures and/or conservative ignition timing advance to avoid the possibility of knocking during heavy load operation under the most arduous environmental conditions with an additional allowance for engine ageing. This conservative operation results in less than optimal power output and reduced fuel efficiency. Production engines using this methodology generally apply significant safety margins, while high performance and improved versions use reduced safety margins in order to achieve higher outputs. Improved older engine types can be given significant and reliable power gains by fitting an aftermarket engine management system equipped with a knock control feature.
Modern production engines usually have an electronic knock detection system that allows only infrequent and light knocking (trace knocking). When trace knocking occurs these adaptive systems reduce ignition timing advance, and may also enrich mixtures and reduce engine load by partial throttling or boost limiting. If adaption is done on a cylinder by cylinder basis, near optimum engine output and fuel efficiency can be extracted for any ambient operating condition or fuel quality.
An unmodified modern high performance engine equipped with an aftermarket engine management system without knock control, is unlikely to safely match original equipment (OE) performance when used with the factory specified fuel. With knock control, OE performance specification is usually equalled and occasionally bettered. Improved modern engines equipped with aftermarket engine management that have a knock control system, allow for considerable extension of engine performance.
•
Increased engine performance - Heavy load operation of your engine with each cylinders ignition timing adjusted to avoid damaging knock. The additional safe ignition timing advance achieved maximizes the engine output. 1
•
Reduced fuel consumption - The additional safe ignition timing advance achieved improves heavy load Brake Specific Fuel Consumption (BSFC). 1
•
Lower exhaust temperatures - The additional safe ignition timing advance achieved lowers exhaust gas temperature giving lower exhaust valve and exhaust system temperatures. In exhaust driven turbo-charged applications reduced temperatures and the reduction of back-pressure associated with the reduced gas temperature extends component life and are responsible for the larger increases of engine output typically seen. 1
•
Improved tolerance to fuel octane rating variation - Near optimum heavy load operation is maintained irrespective of fuel octane rating. 1
•
Improved tolerance to environmental condition variation - Near optimum heavy load operation is maintained irrespective of ambient air intake, coolant, fuel and oil temperatures, ambient air humidity and barometric pressure and engine ageing. 1
•
Diagnostics & Fail safe - Intelligent diagnostic functions support failsafe and limp-home strategies for various abnormal conditions including poor signal quality, sensor or sensor wiring failure.
•
Improved knock discrimination - No compromise methodology used during development of strategies for knock signal capture and evaluation aids discrimination of knock from background noise. Reliable knock detection possible at high RPM. Upper RPM range extension possible when used with broadband knock sensors (relative to use with OEM narrow band sensors).
•
Simplified installation - Autronic Knock control Modules are supplied pre-programmed modules to suit whole engine families. Time consuming tuning of filter frequency, selection of knock detection window angles and knock detection threshold sensitivities is avoided.
•
Interchangeability - These pre-programmed modules suit engine families not just a specific engine. OEM like interchangeability allows engine swaps without Knock Module or ECU adjustment. Automatic cylinder by cylinder adaption allows these pre-programmed modules to deal with the background noise variations associated with engine to engine production tolerances and the fitment of noisy 'engine performance' components without adjustment.
BENEFITS
Notes:
1. When the engine is subjected to 'knock limited' operation
SPECIFICATIONS
Knock 1 |
Processor |
High-Performance 16-bit Digital Signal Controller with integrated Digital Signal Processor (DSP) |
DSP capability |
Simultaneous 1, 2 or 3 bandpass filters with RPM & Crank angle frequency dependent capability. Concurrent signal capture & signal processing |
Input Signal Frequency Range |
1 to 24 kHz |
Input Signal Level Range |
0.05 to 100 volt (Peak to Peak) |
Recommended Sensor/s |
1 or 2 x Broadband Piezo-ceramic Vibration or Cylinder pressure. (usable with narrow band types) |
Indicators Knock Error |
4 x Red Led (either cylinder, cylinder group or bank specific) 1 x Red Led |
Push-button |
Error history reset (Knock 1 - 2CH only) |
Power supply |
Provided by Host ECU Current draw < 100mA |
Operating temperature range |
-25 deg C to +85 deg C |
Storage temperature range |
-25 deg C to +105 deg C |
Dimensions (L x W x H) |
87.0 * 52.5 * 10.0 mm (PCB) 87.0 * 62.8 * 10.0 mm (Overall) |
Weight |
20 gm |
Connector Host ECU Sensor/s |
14 way IDC header
14 way IDC header 3 way header (Knock 1 - 2CH only) |
AUTRONIC ENGINE MANGEMENT ECUS do not provide the level of redundancy required for failsafe engine operation in manned aircraft.
USE OF THIS PRODUCT FOR ENGINE CONTROL IN MANNED AIRCRAFT IS NOT PERMITTED!!!
ENGINE APPLICATION |
SENSOR/S |
TRIGGER LEAD SETTING REQD. FOR HOST ECU (±3 ⁰ BTDC) |
Toyota 1FZFE 6 Cyl |
2 x Broadband |
11 |
Subaru WRX MY 1994 - 2000 |
1 x OEM |
65 |
Subaru WRX / STI MY 2001 - 2005 |
1 x OEM |
88 |
Subaru WRX / STI MY 2005 - 2006 |
1 x OEM |
110 |
Seadoo 4TEC 3 Cyl Jetski |
1 x Broadband |
5 |
Porsche GT3 3.8L |
2 x OEM |
60 |
Peugeot ZJP24 3.0l V6 |
2 x OEM |
67 |
Nissan SR20 T |
1 x OEM |
60 or 110 |
Nissan RB26 T |
2 x OEM |
63 |
Nissan CA18 T |
1 x OEM |
63 |
Nissan Patrol GQ. TB42T |
1 x Broadband |
50 |
Mitsubishi EVO 9 |
1 x OEM |
75 |
Hydrospace 750cc 2 Cyl Jetski |
1 x Broadband |
131.5 |
Honda K24A |
1 x Broadband |
100 |
Ford Falcon XR6 T |
1 x OEM |
80 |
Alfa Twin Spark 2 valve 2.0l 4 Cyl |
1 x Broadband |
59 |
Holden Alloytec V6 (L/R sensors) |
2 x OEM |
54 |
GM High feature V6 (F/R sensors) |
2 x OEM |
54 |
Kawasaki SXR1500 |
1 x Broadband |
20 |
|
|
|
The following calibrations are available from stock. Enquire about other calibrations available on short lead time or provide us with sound recordings of your engine so that a calibration can be generated. Many of our authorized distributors are able to assist with the development of a calibration to suit your application.
KNOCK 1 KIT FOR SM3 & SM4 ECUs
KNOCK 1 KIT FOR PLUG-IN ECUs
KNOCK 1 KIT FOR SM3 & SM4 MARINE ECUs
KNOCK 1 MODULE
PURCHASE OPTIONS